Mining Sequence, Cutoff Grade and Process Optimization using Mixed Integer Linear Programming
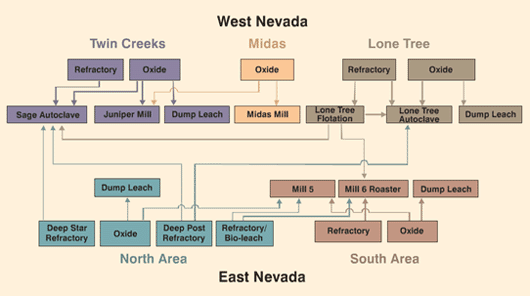
Finding Added Value at Newmont through Large-Scale Mining Sequence, Cutoff Grade and Process Optimization using Mixed Integer Linear Programming
Larry Clark; Mgr., Technical & Scientific Systems Dept., Newmont Mining Corporation, Englewood, CO
Dr. Kadri Dagdelen; Professor, Mining Engineering Department, Colorado School of Mines
Introduction
Despite near-record commodity prices, the mining industry continues to search for ways to maintain profits in these times of steadily increasing energy prices and steadily decreasing grades. The pressure is still on today's miners to continuously improve their operations because they know that one day prices too will drop. Some, however, have seized the opportunity to employ systematic methods to reduce costs and increase the efficiency of their workforce and equipment. As a result, closer attention is being paid to scheduling and the value that could be added by defining the extraction sequence that maximizes the net present value [NPV] of a project. This paper will discuss the challenges faced by Newmont Mining Corporation [Newmont] at its operations and the application of sophisticated software tools and methods in its search of solutions to this problem.
Newmont Operations
Newmont will produce approximately 6 million equity ounces of gold and 300 million equity pounds of copper in 2006 from operations in North America, South America, Africa, Australia, New Zealand and Asia.
North America
At approximately 2.4 million equity ounces of gold in 2005, northern Nevada accounts for roughly 28% of Newmont's equity gold production (Newmont, 2006) and the vast majority of North American production. Ore is both mined and processed at six separate mining centers from a combination of underground and open pit sources (see Figure 1).
Figure 1 - Newmont Nevada Operations
Newmont accumulated these operations through a combination of greenfields development and the acquisitions of Santa Fe Pacific Gold, Battle Mountain Gold and Normandy/Franco-Nevada. Each processing facility, when constructed, was designed to address the needs of its host deposit but once these mines were connected through a common ownership Newmont's technical staff identified value in the cross-shipment of ores between sites (Hansen, 1999). This value is derived from the consideration of the combined set of ore types and available processes across this 'theatre' of operations and the application of the 'optimizer' (discussed later in this paper) to determine the optimal sequencing and material routings. The current cross-shipment strategy is described by the flowchart in Figure 2.
Figure 2 - Newmont Nevada Processing Flowchart
South America
Newmont's South American operations are dominated by the Yanacocha mine in northern Peru (see Figure 3). Yanacocha accounted for approximately 1.7 million equity ounces of gold, or roughly 39% of equity gold production in 2005 (Newmont, 2006). The Yanacocha mine is primarily a gold mine but silver is also recovered. The two recovered metals introduce the need for revenue-based analysis, design and operational (ore) control. Although not as complex as the operations in Nevada, Yanacocha consists of five open pit mines, four leach pads, four waste dumps and a likely new project, Conga, which will bring two new pits into the operation.
Africa
Newmont poured first gold at its Ahafo mine in June 2006. The Ahafo mine currently consists of eight pits that extend roughly twenty miles along the arced strike of the mineralized trend (see Figure 4). To date, 11 ore bodies have been defined with significant potential for further discoveries and extensions to the known deposits at depth and along strike. In addition to the Ahafo mine, Newmont owns the Akyem project in Ghana. Although not located close enough to Ahafo to be operated under common management, it could be considered a future candidate for facility-sharing also.
Figure 3 - Map of the Yanacocha Mine
Figure 4 - Map of the Ahafo Mine
Scheduling Need
Newmont operates several multi-mine, multi-process complexes within its suite of assets. These complexes provide unique opportunities to realize additional value when they are viewed as integrated facilities rather than individual mine sites (Hansen, 1999). But the simultaneous optimization of mine sequences, cutoff grade(s) and process options for these integrated operations is a daunting task that must be done under a myriad of physical and logical constraints. These problems are especially challenging because of the sheer size and complexity of the formulations.
Suitable optimization tools and methods that simultaneously determine the optimal mine sequence, cutoff grades, blending and material routing guidance are needed to analyze these complex properties. These requirements create particularly challenging hurdles for current solution technologies.
Newmont anticipates similar complexities at other operations in the future and recognizes the need to identify and support suitable tools and solution methods for the proper evaluation and maximization of value from its operations.
Mine Schedule Optimization - History
Mine scheduling has been a key component of mine planning for decades if not centuries. Before the advent of computers that now automate the tedious calculations involved, the scheduling task was done by hand. Repeating this manual task until the maximum NPV is found is, for all intents and purposes, impossible given the time and resource constraints imposed on a mining engineering department. The maximum NPV is typically the objective to be optimized. Optimality is defined as (Gershon, 1982):
"...that solution from which it is impossible to achieve any improvement."
Early attempts to develop computer software to solve the schedule optimization problem were hampered by both hardware and software limitations. From a hardware perspective, early generations of computers were large 'mainframe' devices that often filled an entire room, consumed a lot of energy and were very expensive to operate. Despite their physical size, the core memory capacity of early computers was often so limiting that large problems could not be loaded in their entirety and solved. Instead, various simplifying assumptions were made to reduce the problem scale until it could fit within these technical confines.
The literature is rich with examples of different approaches to the optimization of mine schedules. Williams (1974) describes Asarco's recognition of the need for a computer program to solve the scheduling problem. After failing to identify an existing solution, Asarco spent three years with a software contractor to develop a software package that incorporates integer, linear, parametric and dynamic programming techniques to solve the scheduling problem. Because of hardware limits, the final system was restricted to whole (model) blocks with no more than two mineral grades, three rock types and a minimum scheduling period duration of three months. Although no mention is made of execution times it is certain to have been long. The development of this program, however, was significant to Asarco's Mission mine and enabled them to analyze many more feasible alternative mine schedules than before.
Gershon (1982) describes the Mine Scheduling Optimization [MSO] software that was developed using mixed integer linear programming [MILP] methods to address the scheduling problem. Gershon goes on to imply the importance of this subject to the mining industry:
"There is a need for linear programming applications in this area and, when a model is developed that can be applied to many different mining situations, it will be seen that this technique will become more involved with the everyday operation of progressively managed mines."
Gershon's solution aimed to incorporate the ultimate pit limit, blending, transportation (haulage capacity), cutoff grade, plant feed requirements and mine sequencing into a generalized form that could suit many different mining conditions. Gershon employed two external software packages to define (PDS/MaGen) and solve (APEX-III) the LP formulation. Many other examples can be found.
Mine Scheduling History within Newmont
Newmont, like Asarco, recognized the need for more sophisticated software tools to solve the scheduling problem. In the 1980's Newmont formed the Technical and Scientific Systems [TSS] department to develop and support its own software tools for geological modeling, mine planning and ore control. In 1993 Newmont began the development of NPVSCHED, a software program that used a dynamic programming, exhaustive enumeration approach to schedule a series of nested pit phases (Seymour, 1995). NPVSCHED determined the optimal schedule by defining all feasible states (possible schedules) and their associated feasible ancestor states. It then identified the combination of ancestor states that maximized the NPV of a project. The NPVSCHED program was applied to the Batu Hijau project in its early planning stages resulting in improved project economics. It was also applied routinely during strategic planning exercises to provide mine scheduling and stockpiling guidance. The downfall of NPVSCHED was the exponential growth of the enumerations as the problem scale grows with multiple pits, phases and benches.
In 1995 Newmont recognized the need for an expanded schedule optimization tool that could cater to the increasing production of refractory ores coming from the mines and blending requirements of the treatment plants on the Carlin Trend (Hansen, 1999). At that time Dr. Kadri Dagdelen, Professor at the Colorado School of Mines was employed to assist with the development of an MILP solution known as 'The Optimizer' (Hoerger, S. and Et al., 1999). The acquisition of Santa Fe Pacific Gold in 1997 was, in fact, partly justified by the optimizer's identification of $20-$30 million in synergies that would result from an integrated complex of operations in Nevada.
Newmont has also been a user of the industry-standard Whittle™ software since 1989. The Whittle software has been routinely applied, along with the TSS equivalent 'lgnest', to determine and select ultimate pit shells used for budget and reserve designs, (Seymour, 1995b). The Whittle Milawa and Milawa Balance scheduling software has been applied on several Newmont projects in the past 3 to 5 years with various results. On projects with somewhat limited complexity the Whittle software has been used very successfully. However, in more complex situations like those faced in Nevada with multiple pits and and multiple process options and blending requirements an ideal solution has been elusive.
In 2004 Newmont's TSS department approached Dr. Dagdelen again to explore opportunities to participate in the further development of the OptiPit® schedule optimization software. The OptiPit software utilizes a MILP formulation to model complex multiple mines, and processes for multi-time period solutions and is built on the knowledge gained from many years of research and project work performed at the Colorado School of Mines over more than two decades of dedication to mine scheduling including the work done with Newmont in 1995 (Dagdelen, 1985, 1992, 1996, 2004), Akakai (1999), Urbaez and Dagdelen, (1999), Kawahata (2006), Dagdelen and Kawahata (2005 2007).
Other Considerations
Modern schedule optimization tools must, at a minimum, cater to the 'common' requirements of:
- Maximum bench advance (sinking) rates,
- Pit-bench-phase sequence dependencies,
- Rate limits and ranges for multiple mines and processes, and
- Complex mining and processing cost calculations.
For Newmont (and many other mining companies) there are other factors that affect the suitability of the tool in complex environments.
Blending
Blending of material ahead of a processing plant is not new. Perhaps the most well known need for blending comes from the cement industry where kiln feed must be held within very exacting specifications by blending combinations of limestone or chalk, and shale, clay, sand, or iron ore that are mined from one or more quarries near the plant. For Newmont, the segregation of ore by grade range (high, medium, low) has been a common practice aimed at maintaining reasonably constant head grade to the mill. However, with the introduction of the refractory ore treatment plant [roaster] on the Carlin Trend in the mid-90s additional segregation and blending requirements were imposed to maintain sulfur and carbon levels within tight tolerances. Similarly, the autoclaves at the Twin Creeks and Lone Tree mines required consistencies and limits on the chemical properties of feed material.
Today, blending gets even more attention as mill throughput is increasingly modeled as a function of hardness and grindability. The key objective in these cases is to identify the optimal material blend(s) that maximize the value over time from the mill (i.e. $/hr).
Metallurgical Recovery
The ability to model sophisticated metallurgical recovery relationships is also an important aspect to optimization. As processing technology advances so too does the demand placed on mining engineers to model these relationships. Gone are the days of simple recovery relationships and the assumption that these complications can be ignored in the scheduling phase due to limitations in the solution technology. An example of this is the continuous oxidation of sulfide material stockpiled for future treatment through a sulfide process. The material oxidizes as a function of its residence time in stockpile and exposure to air and bacteria, resulting in a drop in recovery when passes through the plant. A strict analysis that incorporates this behavior will provide a more meaningful and realistic result.
Today, Newmont's mining and processing technical staff work together to understand and incorporate these dependent relationships in their project analyses. These joint efforts result in designs that extract the highest value possible from Newmont's deposits.
Process-to-Product Time Delays
The lag in time from placement of material on a leach pad to delivery and sale of a product is typically ignored in the analyses of optimal sequencing and scheduling. It is more common to consider this delay during cash flow analyses after-the-fact by postponing metal production and revenues from leach processes. The optimal determination of cutoff grades and schedules should take this delay into account during the solution step.
Division of Material Flows within a Process
The Sage autoclave at the Twin Creeks mine competes with the roaster in Carlin for concentrates from the Carlin flotation plant. The flotation tailings from the plant are treated through the CIL circuit and then discharged to the tailings impoundment. Satisfying these conditions demands more sophisticated modeling with the ability to split process stream tonnages as they propagate through a circuit.
Load-Haul Equipment Constraints
It is especially important at existing operations to constrain the scheduling problem to the available capacities of existing loading and hauling equipment. Traditional methods provide upper and lower limits on mining capacities but do not address the variation in load and haul cycle times that occur because of rock hardness or location. The optimization must be able to quantify the equipment time needed to achieve the proposed material movement and strictly limit the schedule to this constraint. By providing equipment hours as an attribute in the model and restricting the attribute to specified fleet capacities, the engineer can be more confident in the resulting schedule. In addition, the engineer can quickly assess the impact of step changes in the equipment fleet.
Waste Rock Scheduling
Scheduling of waste rock is often a critical path item with dam and plant site construction being dependent on the timely delivery of fill or foundation material. The solution methods and tools must support the need to mine waste rock to satisfy these needs and in proportions that ensure compliance with waste rock encapsulation requirements. In addition, the scheduling of waste production must cater to the backfilling of pits and the associated sequencing constraints to avoid dumping on top of active mining areas.
Royalty Payments
The tracking and reporting of royalty liabilities is a key concern for Newmont and most other mining companies. At the analysis stage these royalties have an impact on cutoff grade and, therefore, optimal sequences and destinations. The solution method must cater to this need and identify the optimal schedule given these incremental costs.
Multiple Products
Newmont is primarily a gold producer but several of its operations recovery multiple saleable products. The Phoenix mine for example produces copper, gold and silver. The Batu Hijau mine produces copper as its primary metal but also recovers significant value from gold. The combination of payable products requires additional sophistication in the application of revenue-based models and cutoff grade guidance.
Non-linear Grade Estimates
Newmont has used a customized approach to multiple indicator kriging since the early '90s (Hoerger, 1992). As with other non-linear methods, the resulting block model cells contain a distribution of material grades rather than a single estimate. The scheduling solution must be able to accept multiple "packets" or "parcels" of information describing each block's grade distribution. Additional complexity exists when multiple grades are modeled.
Multiple Time Periods
It is important that the scheduling problem described here be modeled and solved as a multiple time period schedule optimization problem since attacking and solving the problem one period at a time or 2 or 3 periods at a time is not acceptable. The scheduling solution must be able to look ahead 10, 15, even 20 years or more depending on the life of the project to determine schedules during the beginning of the project.
Large Data Sets
Newmont operates large mines with multiple pits and accompanying large resource models. Block models can often contain in excess of one million blocks. Although scheduling is not done on a block-by-block basis, the pre-and post-processing required by the optimization solution can become time consuming and put additional requirements on computer hardware.
Technology Development
Addressing the Complexities
Clearly there are many complications that must be addressed by a schedule optimizer. In its search for a solution, Newmont has identified a number of gaps in existing technologies that have only partially been addressed. These are:
- Performance - the ability to cater to large scale problems in an acceptable timeframe,
- Generality - the solution must be easily adapted from one project's conditions to another,
- Usability - the solution must be reasonably intuitive and flexible for the user, and
- Comprehensive - the solution must address all the complexities discussed.
During several internal evaluations, the OptiPit® software demonstrated its capacity as an effective schedule optimizer to address the majority of the scheduling issues raised here. It should be noted, however, that the OptiPit software does not include pit limit analysis or phase optimization tools in its current state. However, it has provided promising results and guidance and could, with additional development, become more widely used within Newmont.
Developing the Solution
Each of the products in use today by Newmont addresses a subset of the requirements but none delivers a total solution. As a result, Newmont has been participating in the improvement of the OptiPit® software at the Colorado school of Mines and encouraging and supporting its commercialization through OptiTech Engineering Solutions LLC of Golden, Colorado. At the same time, Newmont's mine engineers continue to explore and work with the available commercial solutions. Ultimately, Newmont believes that a competitive commercial software market will drive innovation and new product development. However, the market for these software solutions is very small and price-sensitive. Because software companies providing optimization solutions are small in comparison to large mining companies, they often have difficulty funding research to develop new solutions. They must balance the risk to their company, their commitment to their current client base and the need to develop new solutions. Reformulating a main component or developing a new approach is not often chosen, particularly when an existing solution 'works'. By participating in the advancement of the science through OptiPit®, Newmont hopes to extract value today and let the resulting competition stimulate more creativity for the future.
Sustaining the Solution
Finding the optimal production schedule for an operation can result in the savings or generation of millions of dollars. To realize this value a systematic application of optimal mine scheduling policies must be practiced. This can be achieved most directly by defining optimization as a key business process. The importance of the task then demands a sufficient commitment to training and the implementation of a 'system' to aide the users. Ultimately the solution may consist of a pair of products whose strengths when used in parallel help to corroborate outcomes and/or identify further opportunities.
Future Directions
Performance
The Achilles' heel of the current schedule optimization tools is performance. Cleverly reducing the problem scope (without impinging on the optimal solution) while at the same time applying faster computers will together achieve step changes in performance. Microsoft's impending release of the 64-bit Vista™ operating system and its ability to address a much larger memory space will allow much larger models to be solved. Combining this with steady improvements coming from commercial linear programming solvers will also significantly speed the overall performance of the systems.
Data Security and Management
The use of SQL Server and Oracle to store and protect data is gaining momentum in the mining industry. These system's capabilities, both from end-user and software developer perspectives continue to improve. They provide robust security models and data replication/synchronization and are widely accepted as backbones for large enterprise resource planning [ERP], accounting, payroll, and human resources systems. They have already begun appearing in mine planning and scheduling systems due to the vast stores of sensitive data these systems require.
Ease-of Use
Sophisticated analyses require sophisticated tools. Typically this results in software that is challenging for the infrequent user. As better software development tools and standards appear it becomes easier to build 'wizards', context-sensitive help and other features that address usability. This has helped diminish ease-of-use problems but close attention must still be paid to data flow and interaction with the user. Scripting or macro facilities that automate some of this interaction and execute the software also can lead to a more powerful and well accepted package.
Conclusion
Through the systematic application of mine schedule optimization tools Newmont is identifying added value at its operations. The current state-of-the-art tools, however, lack the specific features needed at its more complex project's to optimize infrastructure size, mining and/or processing rates and cutoff grades. Ultimately the objective of these tools is to assess the optimal scale of a project and provide operating guidance for its mines.
Newmont is participating at the Colorado School of Mines to advance the state-of-the art in schedule optimization to cater to all the requirements of its operations. By applying sophisticated software tools in combination with defined processes, procedures and training, Newmont will maximize the value it extracts from its assets and conserve its scarce manpower and valuable capital. Newmont is one of many companies that participate in the advancement of technologies through research and development. It is hoped that through this discussion others may recognize the value they may be missing and participate in the development of the tools as well. With its commitment to the technology, a growth of internal knowledge and expertise will be seen and Newmont will reap the rewards at its bottom line.
References
Akaike, A., 1999, "Strategic Planning of Long Term Production Schedule using 4D Network Relaxation Method", Ph.D. Dissertation, Colorado School of Mines, Golden, Colorado
Dagdelen, K., 1985, "Optimum Multi-Period Open Pit Mine Production Scheduling", Ph.D. Dissertation, Colorado School of Mines, Golden, Colorado
Dagdelen, K., 1992. Cutoff Grade Optimization, in Proceedings, 23rd APCOM, University of Arizona, Tucson(Ed: Y.C. Kim)
Dagdelen, K., 1996, "Formulation of Open Pit Scheduling Problem Including Sequencing as MILP", Internal Report, Mining Engineering Department, Colorado School of Mines, Golden, Colorado
Dagdelen, K., Topal, E. and Kuchta, M., 2000, "Linear Programming Model Applied to Scheduling of Iron Ore Production at the Kiruna Mine, Sweden", Mine Planning and Equipment Selection, pp. 187-192
Dagdelen, K., 2004, "Open Pit Optimisation - Strategies for Improving Economics of Mining Projects through Mine Planning", Orebody Modeling and Strategic Mine Planning, Perth, WA, Australia, pp. 21-24
Dagdelen, K. and Kawahata, K., 2005, "Cutoff Grade Optimization under Complex Operational Constraints for Open Pit Mines", SME Annual Meeting, Salt Lake City, Utah (Presentation)
Dagdelen, K. and Kawahata, K., 2007, "Value Creation through Strategic Mine Planning and Cutoff Grade Optimization", SME Annual Meeting, Denver, Colorado, (forthcoming)
Gershon, M., 1982. A Linear Programming Approach to Mine Scheduling Optimization in Proceedings, 17th APCOM, Colorado School of Mines (Ed: T. Johnson, R. Barnes)
Hoerger, S., 1992. Implementation of Indicator Kriging at Newmont Gold Company in Proceedings, 23rd APCOM, University of Arizona, Tucson(Ed: Y.C. Kim)
Hoerger, S, 1999. Long Term Mine and Process Scheduling at Newmont's Nevada Operations in Proceedings, 28th APCOM, Colorado School of Mines (Ed: K. Dagdelen)
Hansen, B.D., "Newmont Cuts Costs and Increases Reserves at Carlin" Mining Engineering, October 1999.
Hoerger, S., Hoffman, L., Seymour, F., 1999, "Mine Planning at Newmont's Nevada Operations," Mining Engineering, October 1999.
Kawahata, K., 2006, "A New Algorithm to Solve Large Scale Mine Production Scheduling Problems by using the Lagrangian Relaxation Method", Ph.D. Dissertation, Colorado School of Mines, Golden, Colorado
Lane, K.F., 1988, The Economic Definition of Ore, Mining Journal Books, Ltd., London
Newmont 10-K/A SEC Filing, 2006
Seymour, F., 1995. Finding the Mining Sequence and Cutoff-Grade Schedule That Maximizes Net Present Value in Transactions, Society of Mining Engineers AIME, Vol. 298, December 1995, pp. 1880-1884
Seymour, F., 1995. Pit Limit Parameterization from Modified 3D Lerchs-Grossmann Algorithm in Transactions, Society of Mining Engineers AIME, Vol. 298, December 1995, pp. 1884-1889
Urbaez, E. and Dagdelen, K., 1999, "Implementation of Linear Programming Model for Optimum Open Pit Production Scheduling Problem", Transaction, SME, Vol.297, pp1968 - 1974
Williams, C., 1974. Computerized Year-by-Year Open Pit Mine in Transactions, Society of Mining Engineers AIME, Vol. 256, December 1974, pp. 309-317